Interview with a Heavy-duty Diesel Engine Part
by L.A.SLEEVE
Article by Steve Scott. Thanks to the ‘AERA’ and “Engine Professional” magazine. (reprinted by permission)
Some engine parts are always looking to be in the limelight, while others quietly do their jobs unnoticed in the background. We are hoping to interview one of those behind-the-scenes parts – the cylinder liner.
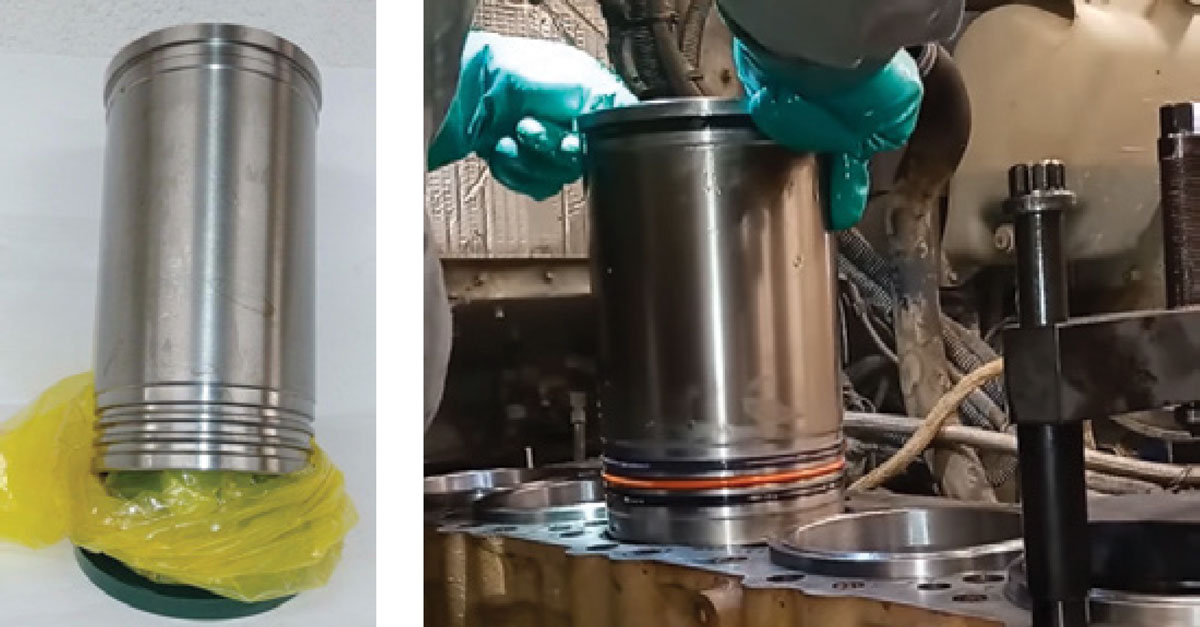
Q: Excuse me, Mr. Cylinder Liner, would you mind answering a few questions?
A: I suppose – what do you want?
Q: Why are you so defensive? You seem to have a chip on your shoulder.
A: Chip on my shoulder? That’s a poor pun, and not a good way to start a conversation.
Q: Sorry I didn’t mean that figuratively.
A: Okay, look, I may be a major engine component, but I am not like some of my colleagues that crave attention. I don’t care to be in the spotlight and I’m not photogenic.
Q: I don’t understand.
A: Okay, take pistons for example, there’s some loud mouths. Always bragging about their compression ratios, bowl designs, and some Wizz-bang coatings. Aluminum, articulated, one-
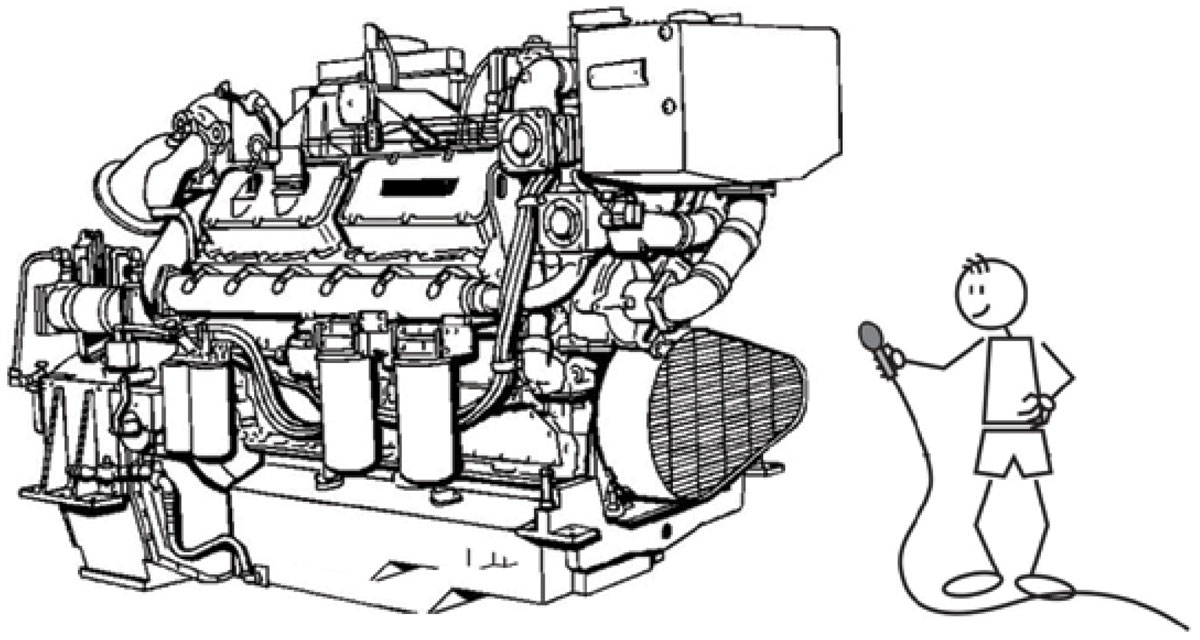
piece, welded steel designs blah blah blah. And the three amigos (piston rings) aren’t much better. They brag about their tension, exotic coatings, keystone vs rectangular and how they control oil consumption. Let me tell you something, they transfer most of the heat in the cylinder to me! Yes, they scrap excess oil from my surface, but if I didn’t retain enough oil film to protect us, we would all be dead. Pistons and rings have seen their share of changes, horsepower and temperature have multiplied, but as soon as that combustion happens, they both race to the bottom, and yet I’m standing right here in place.
Q: No offense, but you are made of cast iron—right?
A: Yes, but I’m not your grandma’s cast iron skillet. I am not a cylinder sleeve, which are typically steel. Sleeves are installed in parent bore blocks. I am what is called a wet liner. My purpose is to serve out my service life in a heavy-duty diesel or gas engine and then be replaced by another. By design we allow the engine to be rebuilt multiple times. I am typically made of ductile cast iron, which is a specific grade of cast iron. Magnesium and other alloys are added to increase strength and make me more impact-resistant. I am made from centrifuged cast material, where molten metal is poured into a spinning die and solidifies over time. The high velocity spins the heavier material to the outside of the die producing a consistent material structure and reduces defects. The casting matric microstructure accounts for lamellar pearlite,

free ferrite and carbides and the graphite type and size. I am induction hardened to give the longest service life I can. Some of my colleagues may be made of different material, by different processes, and coating may be applied for some applications, so you would need to ask them your questions also.
Q: But, why cast iron?
A: Cast iron has been a proven material for cylinder liners long before you were born. Strong, durable, absorbs vibration, resists heat and helps maintain a protective oil film. Cast iron has been a proven material for decades.
Q: So, you are prone to cracking?
A: All metal is prone to cracking, but the alloys added to my makeup reduce that chance. Besides, most of the time one of us cracks vertically, it’s due to impact damage and horizontal cracks are likely due to fitment issues. We usually still catch the blame but it’s rarely our fault.
Q: Aren’t you susceptible to cavitation?
A: Yeah, and black cats are bad luck, and you shouldn’t go swimming right after you eat. Cavitation is not a cause – it’s a result. It’s the result of air bubbles exploding on my outer surface in the coolant cavity. Weak coolant, harmonic vibration and introduction of air in the cooling system are the main causes.
Q: What is your role in oil consumption?
A: I am uniquely plateau-honed. Plateau honing finishing is controlled by five different parameters:
1) Rk: Core depth. Depth of roughness core profile.
2) Rpk: Reduced peak height. Average height of the protruding peaks above the roughness core profile
3) Rvk: Reduced valley depths. Average depth of the profile valleys projecting through the roughness core profile.
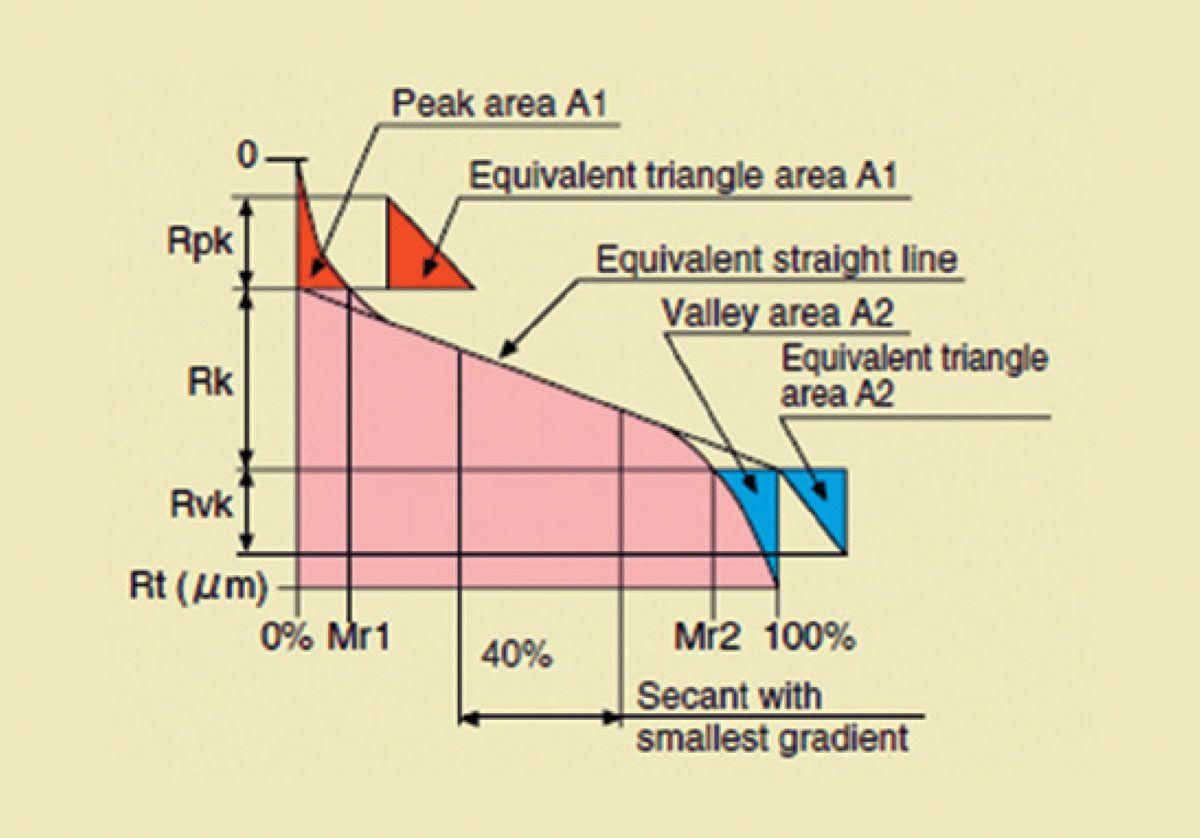
4) Mr1: Material portion, a level in percent (%), determined from the intersection line that separates the protruding peaks from the roughness core profile.
5) Mr2: Material portion, a level in percent (%), determined for the intersection line that separates the deep valleys from the roughness core profile.
And, the inside bore is induction hardened to increase service life.
Q: Whoa, I didn’t realize it was that complex.
A: Trust me, if you ask the engineering or manufacturing departments for more information, your eyes will really glaze over.
Q: What else can you tell us about?
A: Roll-burnishing is something a lot of people don’t know about. It’s a process of burnishing under the flange to add strength.
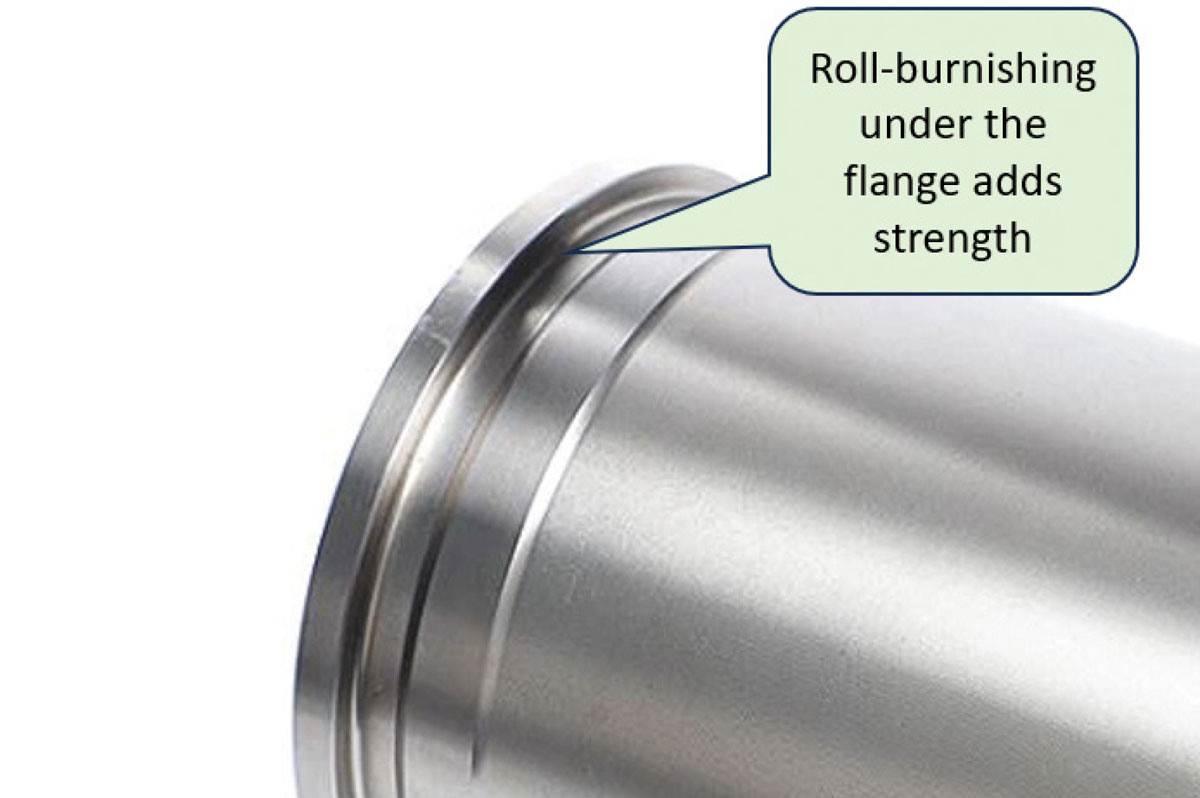
Q: What about…
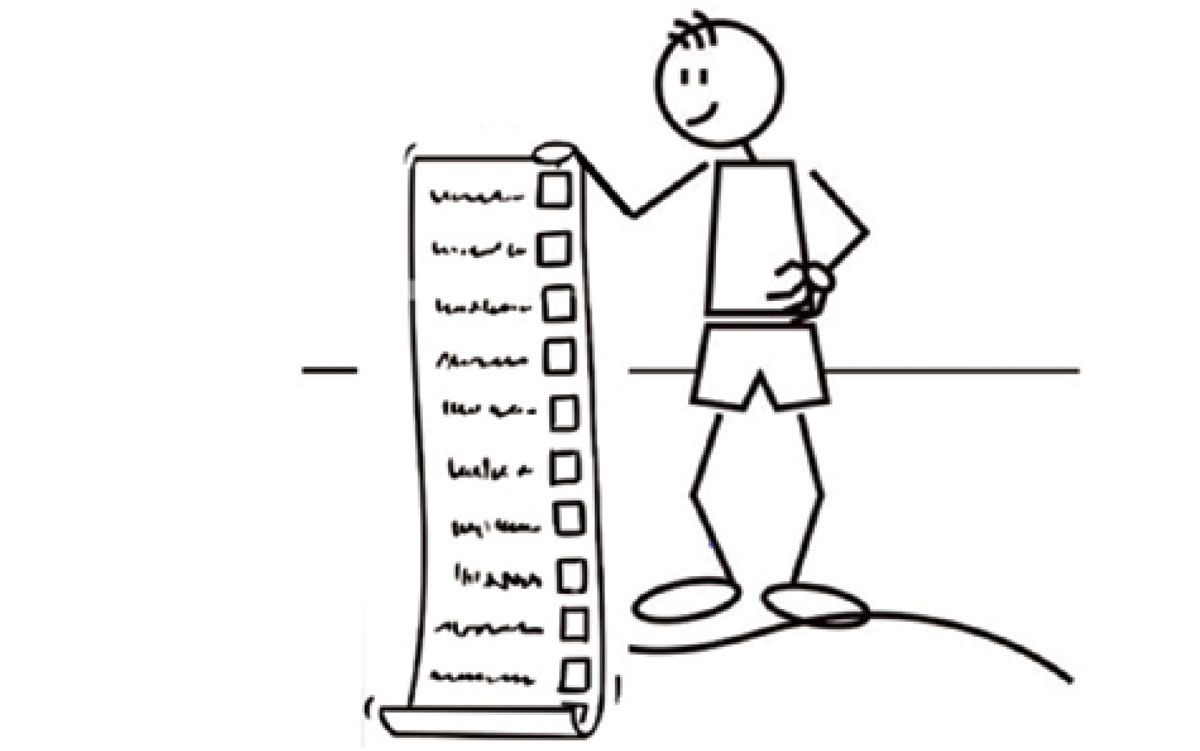
A: Whoa, stop, stop, stop. I’m getting sunburnt from being in your limelight. I just want to go back in the cylinder block to do my job. You should go pick on valves, injectors, or turbos – those guys are always starving for attention and posing for the cameras.
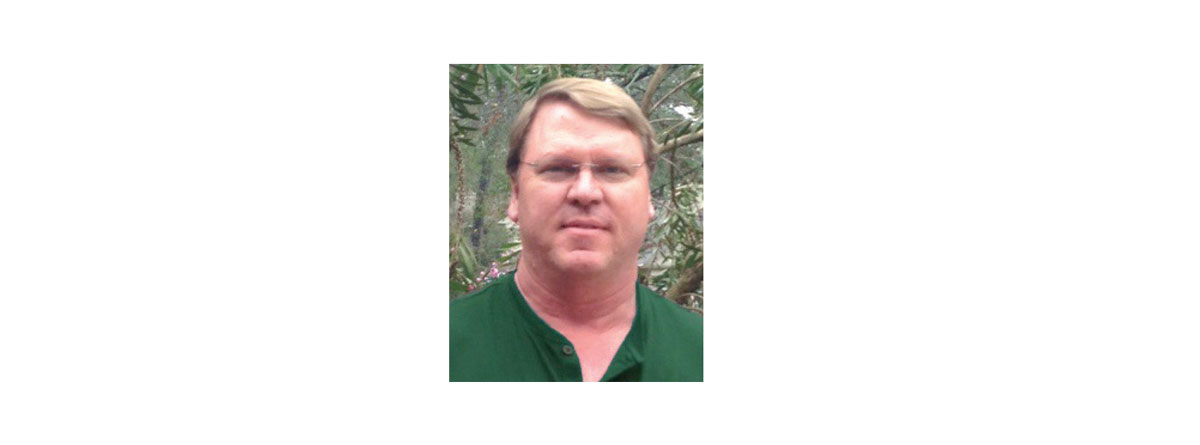
Steve Scott joined the service department at IPD in 1982, working with parts, service and sales for a variety of equipment, diesel, and natural gas engines. Since 2004, he has been the director of product development and technical support for IPD.
Thanks to the ‘AERA’ and “Engine Professional” magazine. (reprinted by permission)